Can the maritime industry heal itself?
08 Mar 2018 Reading time calculated text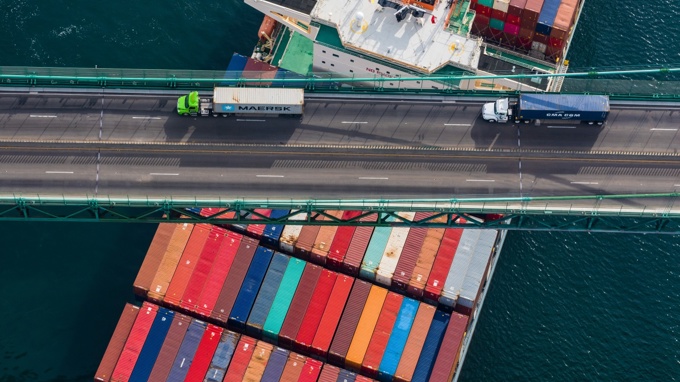
Maritime transport, the backbone of global trade, transporting over 90 percent of the world’s cargo, is suffering. Two key problems are a growing greenhouse gas (GHG) emission issue, which must be brought under control and a prolonged period of unsustainably low profits for stakeholders.
Could there be a way that the industry can systemically and sustainably heal itself? Can the industry develop smart cargo handling systems that so dramatically improve cargo transportation efficiency that the growth in GHG emissions is also stemmed? MacGregor believes it can.
During his presentation at the January Smart4Sea conference in Greece, Marcus Ejdersten, Director, Strategic Marketing, MacGregor, focused on the need for intelligent solutions to increase new and existing vessel’s actual cargo intakes and lower the emissions they generate per tonne of cargo carried.
Even though the maritime shipping industry is by far the most energy-efficient method for transporting cargo, according to the European Commission, it emits about 1,000 million tonnes of CO2 annually, about three percent of global emissions and this is expected to grow.
The industry has lost its way
“In the race for larger, cheaper vessels the industry lost focus on any long-term goal of sustainable efficiency and a vessel’s lifetime earning capability,” says Mr Ejdersten. “Recent MacGregor research estimates that annual losses from underperforming container cargo systems stand in excess of 10 billion Euros. We found that multi-purpose vessels can take up to three years in operation before performing acceptably after delivery from the shipyard, and that the average cargo utilisation rate of Baltic Sea multi-purpose vessels is lower than 40 percent.
“Furthermore, a MacGregor RoRo logistics study showed a 500 percent performance gap between the best and worst vessel turnarounds in port.
“P&I Clubs add to these statistics, indicating that vessel mooring system designs are not fit for active duty, with one to two percent of vessels losing their anchors every year. No one would accept an equivalent rate of tyre loss from cars on the highway, so why do we?”
Waste in the value chain
“We see significant waste in the value chain, stemming from insufficient information sharing, generic processes, and outdated and ingrained bad working practices. A key problem is the current obsession of shopping around for the lowest-cost components. When these are brought together in a ship as part of a wider system, they almost invariably never deliver the same yields as a ship designed with its end high-performance target in mind.
“All these elements drive inefficiencies and also jeopardise crew and cargo safety as a result of a weak safety culture, complacency and short-termism,” he continues. “Together they drag down the attractiveness of our industry, but we need to recruit the best talent from the next generation to move forward.”
Mr Ejdersten also highlights that the value gained from energy-efficient vessels does not always translate into an advantage. “An interesting study from shippingefficiency.org found that energy efficient vessels do not deliver any higher charter rates to their owners, and neither are they operated differently to the average vessel; value is not captured or given away. So something needs to change; no one is going to ask our permission before they disrupt us.”
Far-reaching potential
The industry has a lot of potential particularly stemming from underperforming systems and processes. “We are starting to rectify some of these systems, solutions are already being used today and can be deployed on thousands more vessels in the future.
“To capture value, we need to focus on the lifecycle earning potential of the vessel, not only on initial CAPEX,” he explains. “We need to identify key stakeholders at an early phase and involve them for collaboration before any critical design decisions are made that could limit the lifecycle earning potential. It is also about building vessels again around their intended purpose, to transport cargo.
“Let us put the cargo back in the centre again, because it is not about the vessels, but the cargo. A standard ship design is not competitive enough; we should have a holistic approach to systems on board. It is no longer enough to optimise components one at a time; you need to optimise systems as a whole. It is also not enough to have the highest capacities on paper, when in reality, under realistic seagoing conditions and actual cargo profiles, these figures fall far short.”
Targeted innovation improves impact
“Looking ahead, there is the need for a mindset change,” Mr Ejdersten stresses. “We need to enhance targeted innovation, because innovation for innovation’s sake does not guarantee impact. Innovation cannot only be driven by internal ideas or the availability of new technology, innovation should be driven by clearly defined problems, so let us start collecting the problems as well as the ideas.
“We must start to value a good problem perhaps even more so than a great idea. However, let us not forget that it is not only about solving problems with new equipment or products; we must also enhance and appreciate innovation in processes and services. You need to master all elements to make an impact over the entire lifecycle.”
Practical solutions exist for every sector
“I understand that these ideas are sometimes hard to turn into practical solutions, but I can tell you what one of them looks like for the containership market. MacGregor has developed a concept, called a Cargo Boost, applicable to both new and existing vessels. At the core of the concept is bespoke software, which analyses and simulates your vessels’ operations. We can simulate your container vessels over several years and rotations before applying different design concepts and variables such as cargo profiles, speeds and ports of call. These help us and our customers understand the impact that every small design decision has over the lifetime of a vessel.
“This is not about just selling equipment to shipowners; it is about fundamentally improving processes, cargo handling arrangements and training, and staying with the customer to monitor that it really benefits from the impact of the value gained and that the whole business and its stakeholders understand how to get best use of the new vessel.”
MacGregor is working on similar concepts for every ship sector. For the breakbulk segment, it is focusing on smarter stowage planning using various techniques, including software algorithms for optimisation. “In 2017, we undertook a proof of concept for one customer and were able to achieve a 10 percent gain in cargo carrying in minutes, rather than the normal full day of planning. We are still developing this product, but imagine the impact on your fleet: either you are able to carry 10 percent more payload or have fewer vessels carrying the same capacity.”
To assist the RoRo and pure car truck carrier (PCTC) sector, in 2017 MacGregor acquired a cloud-based collaboration platform, which it will continue to develop. It enables shipowners and operators to capture and analyse transparent data from all stakeholders involved in the logistics chain, so that fact-based decisions can be made, removing the need for best guesses. “After a one-year pilot study on a relatively small fleet, we identified several million Euros worth of waste that could be tackled together with stakeholders.
“So, there is huge potential across the maritime industry and there is lot of value to capture. It is not necessarily that we have to wait indefinitely for new technologies, but working with what we already have available. There are going to be different ways to continue, but I think one common denominator is that no one can do this alone," Mr Ejdersten concludes.
We need to collaborate more, so the next step is to cooperate; let’s co-create a better future.
- Marcus Ejdersten