Make friends with your digital twin
18 Jan 2023 Reading time calculated text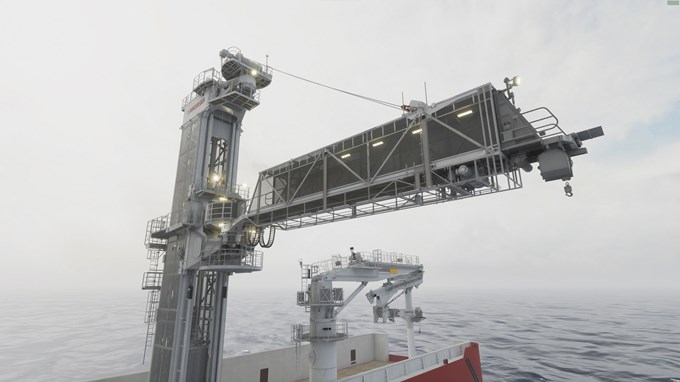
With equipment installed on the equivalent of every other ship at sea, MacGregor’s marine and offshore ambitions to exploit digital twin technology at scale are as achievable as they are understandable.
Like many of the digital terms entering the marine and offshore lexicon, gains associated with the ‘digital twin’ have quickly become slippery due to multiple interpretations. But a technology with deep consequences for design, operations and maintenance cannot be allowed to slide into the shallows of the maritime buzzword, say Dennis Mol, Vice President, Technology & Sustainability, and Bhavik Thakker, Director, Digital Solutions, MacGregor.
This is one reason MacGregor recently formalised the Digital Twin part of its digital services offering. Another is that the group has already proved a front-runner in securing safety, productivity and sustainability gains by developing real-time digital processes to support the marine cargo and offshore load handling equipment it delivers.
“Rather than talking up potentials, we have evolved a set of cases to demonstrate the purpose of using a digital twin in different scenarios,
and the benefits of calculating, simulating and analysing what is feasible for equipment based on data from the operating environment,” says Thakker.
MacGregor’s conclusion is that digital twin technology has value for marine and offshore customers at every stage of its product and service offering: from the product concept stage, to design and engineering verification, testing and sea trials, training, operations and maintenance.
Alternative realities
“Data that is ‘engineering-level’ accurate allows a digital twin to simulate the real time dynamics of an actual vessel in its environment,” explains Mol. “This creates analytical power that goes beyond theoretical modelling. A designer can evaluate the impact of an integrated equipment configuration at the pre-development stage, for example, and work to refine control systems in advance to benefit the whole.”
Allowing the user to try-out a new design is empowering for the customer and invaluable for the engineer – both as a way of exploring and predicting behaviour, and as a tool to get things right the first time and avoid cost overruns. For MacGregor, the benefits of using the digital twin are available from a product’s conception to the end of its operational life, Mol stresses.
“Working with accurate specifications and real data, we can use the digital twin for FEED studies and rapid prototyping in the idea development phase, and present the customer with interactive ‘almost-real’ experiences,” adds Thakker. “Later in the process, the technique allows us to optimise the general arrangement, choose the right equipment combinations, develop realistic structural analysis, verify the design, and simulate and analyse work processes.”
Behind every good twin – a better twin
“MacGregor has already used a digital twin in key product developments,” says Mol. “Its in-house developed ‘C-how’ simulation technology has been deployed to de-risk the engineering phase, verify the design in different on-deck scenarios and optimise operability.”
In one case, a shipyard used a digital twin to simulate control responsiveness of a MacGregor davit system during boat launch and recovery, in order to verify the maximum wave height limit. In another example, using the technique in the product test phase enabled dynamic vessel motion modelling so that an owner could verify that a gangway designed for the bow of a vessel would operate safely at greater wave heights.
For operational purposes, one MacGregor customer made use of a digital twin to maximise the weather window within which subsea equipment could operate, while another developed new subsea crane operating guidelines after an incident involving a mis-timed change in mode.
Data-driven lessons
“The data analytics capabilities can be used for predictive maintenance planning and to anticipate failure and repair needs for critical equipment well in advance,” he says.
But the usefulness of the digital twin for worldwide maritime industries is not limited to machinery. “The experience of using the digital twin also takes training using simulation to a new level,” adds Thakker.
“In fact, the best point of delivery for the data-driven lessons that enhance equipment efficiency is to the people using it. Training needs to be delivered in the most effective way, and e-learning, scenario-based simulations, analytics and immersive augmented reality-based methods create a powerful mix to get the message across on standards to office-based and shipboard personnel alike.”
A digital twin-level of simulation accuracy makes high-fidelity training more affordable, based on MacGregor’s heritage and continuing role as a global supplier of handling equipment.
In a fast-changing scenario, MacGregor is already trialling the use of the digital twin technique for an augmented reality-based pilot covering air compressor maintenance sequencing, says Thakker, but his preference is to focus on gains already won.
“Getting that real-time feel and having the ability to simulate how equipment actually responds in an emergency situation results in a much steeper learning curve for the user,” he says. “If an incident has occurred in the past, we can just play it back using a rich visual format, see how the guys respond and then train them on what they could have done better or patterns to look out for.”
MacGregor is on the verge of delivering a new portable simulation-based offshore active heave compensation crane training package which uses digital twin capability to an offshore support vessel operator, he discloses, based on a rental and software licensing agreement.
“Our experiences with digital twin technology have allowed us to mature and formalise our approach across the entire scope of our activities - from design and engineering to testing, verification, training, operational support and maintenance,” adds Thakker. “And the more we learn, the clearer the benefits for our customers become.”
Caption for the photos: Images from a simulation utilising the digital twin technology.
This and further articles in our latest edition of MacGregor News include:
- Sustained demand for sustainable PCTC equipment
- MacGregor’s electric solutions improve sustainability and profitability
- Make friends with your digital twin
- Introducing the new captain of MacGregor’s service business
- Service exceeds expectations for China’s new generation drilling rig
- Support for safe, efficient and sustainable research